Hot stuff – we're trialling thermal repairs on roads around Bucks!
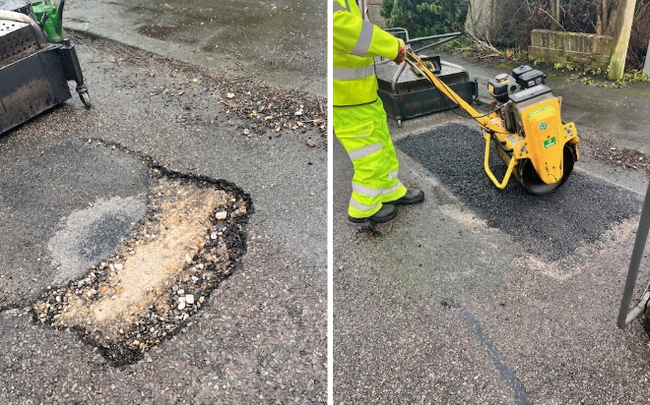
Our highways team has been trialling a new technique for repairing potholes and road defects, called a ‘thermal repair’ technique.
We are always looking to explore innovative solutions to maintain the highway network, which support our value for money approach to work.
Recently, our highways team has been trialling a new 'thermal repair' technique for repairing potholes which utilises nu-phalt™ technology. An example of where we’ve been trialling this technology is on Rose Drive, Chesham.
This technique requires using a portable thermal heater machine. The machine is placed over a pothole, or another road defect, and the area is heated to 200°C (+/- 30°C). Once that area of road has melted, the operators cut an area 50mm in from the repair edge - meaning we actually make the defect slightly larger before fixing it. This is so we can deliver a strong, seamless joint between the new material and the existing road material which is being reused and recycled around the defect.
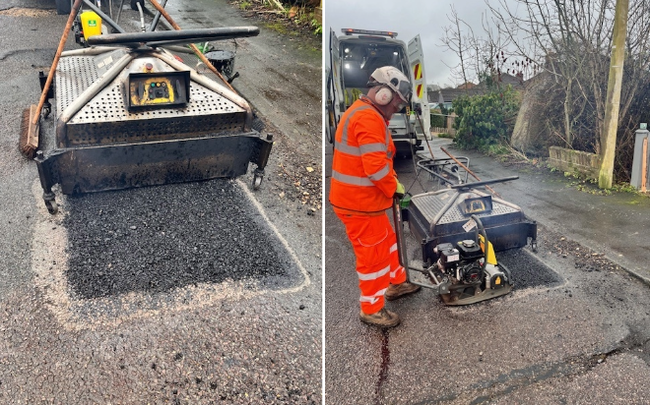
Portable thermal heater machine, heating up the defect area.
The next step is to add a high-grade bitumen emulsion to the area in need of repairing.
A bitumen emulsion is a liquid composed of three liquid materials: water, bitumen (a sticky, black, liquid which comes from petroleum) and an emulsifier (a substance which stabilises the emulsion, allowing the liquids to be "mixed" but preventing the liquids from dissolving into one another).
The emulsion is evenly mixed through the melted road surface material to create a consistent and even base. The emulsion increases the repair areas' bitumen content to levels that are comparable to the bitumen content in brand new materials. This clever process means that no material is taken from the repair – everything is recycled in-situ, meaning there is no waste.
To complete the process, additional new material (called nu-phalt asphalt) is then heated in the Highways vehicles' "on board hot box" before being transferred to the repair area and compacted using a roller. An infrared thermometer is used to check the temperature of the repair area. The material temperature should be typically between 70-100°C to provide the best compaction conditions.
For more detail on how thermal road repairs work, take a look at nu-phalt™ website.
For more detail on how thermal road repairs work, take a look at Nu-phalt™ '6 Stage Process'.
There are a number of benefits when using the thermal repair method. These include:
- The nu-phalt™ Thermal Road Repair System has been proven to reduce costs by up to 40% when compared to traditional pothole repair methods.
- Less materials being used for repairs because the existing road surface is recycled during the repair. On average, a patch defect repaired using the thermal method uses 50% less material than traditional methods, such as plane and patching.
- There is zero waste to the thermal repair method, meaning old material does not need to be sent to landfill.
- The speed and efficiency of the process ensures it uses significantly less energy than conventional alternatives.
- The repairs last longer as the new material binds to the existing road surface, preventing water from seeping under the tarmac.
There are some constraints to using this method. Due to the amount of time this process takes, the method is best used on a road that has multiple repairs needed, to maximise efficiency. Therefore, it wouldn’t be beneficial to repair a single pothole with this technology. Additionally, as the machine is electric, it can only be used in light rainfall, which makes it tricky to use during periods of poorer weather.
Despite the few constraints, the thermal repair method and the portable thermal heater machine is another available tool for our teams to deploy to continue fixing road repairs. Using all available methods (both traditional and innovative), we have now repaired over 60,000 potholes / defects since the formation of Buckinghamshire Highways on 1 April 2023.